The Challenge of Chassis Shortages
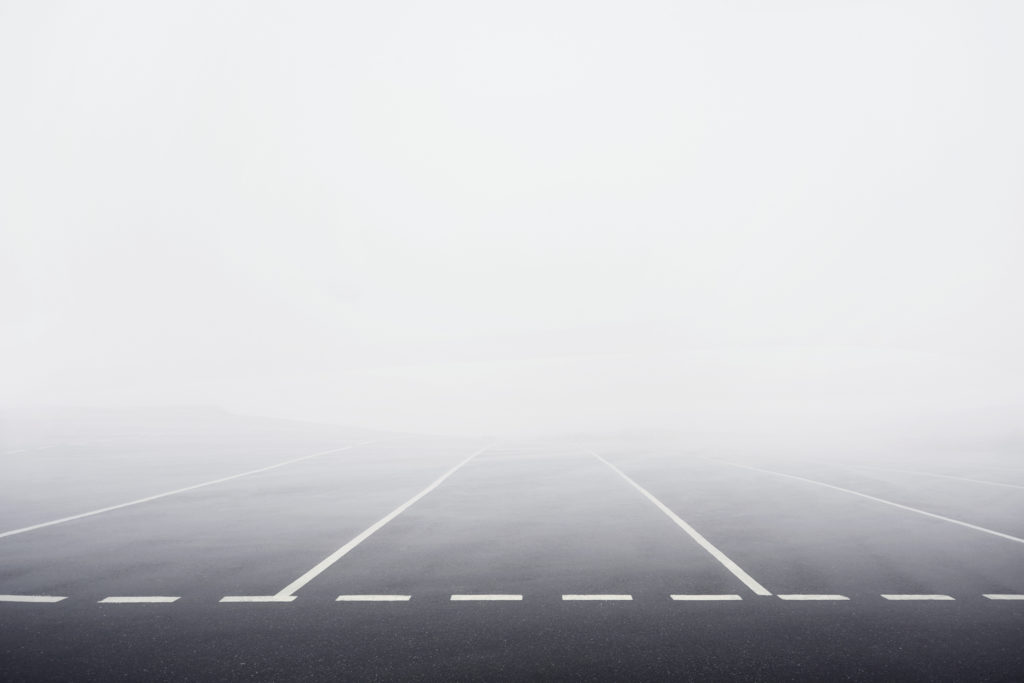
Rail congestion and a shortage of chassis are making it challenging to move containers through a tight peak season. Trapped under a mountain of imports, chassis are often stuck under containers waiting to be loaded on the rail or ship, unable to move until the stack is handled. Analysts expect the shortage to last until 2023 as the lead time for new chassis is between 9-12 months and dependent on whether manufacturers are making the 20’ or 40’ marine chassis or 53’, an issue that came up in early January when 53’ chassis were rare.
Though we’ve been talking about the container part of equipment imbalances, the chassis issue started in 2020 as the US placed retaliatory duties on Chinese goods, ending the 90% of chassis imports that originated in China. Shippers are still battling against the shortage and other equipment problems caused by trade policy.
Congestion on the rail has led to a bottleneck of containers and stacks of boxes with cargo hidden deep in the bottom, unable to move due to the sheer quantity of shipments waiting for transportation. At the ports, rail delays complicate the bottlenecks as few containers can leave the terminal to load on the trains because of congestion.
Chassis at the Ports of Los Angeles and Long Beach are showing between seven and nine days of leave before they’re returned, which encompasses the containers that are picked up and held, on a chassis, outside a warehouse where there is no space to unload the box. Warehouse space can be much more difficult to secure than just paying the fees on shipments that come, in some cases, in their very own storage space. With retailers hurrying to stock up on inventory for the coming holiday season, there’s little chance that the situation will self-sort before the shopping season kicks off.
Oddly, in the most humorous version of the word, there are also issues that some are having returning empty containers as there is no room in the yard for empties because they can’t get the full containers picked up or don’t have chassis to send the overage of empty containers out to fill and export. It’s a difficult situation that requires a ballet level of training to navigate.
Flexibility, advanced notice, and planning are the keys to managing this situation for everyone with equipment issues. The more notice we can give carriers, the better our chances of securing the required equipment. For now, we can no longer just pop a call into a carrier pool and expect a same-day drop as we did in the past. In some cases, carriers need upwards of two weeks to fill an order, and frequent delays, rescheduling, and cancellations are commonplace. Patience and flexibility are the most important part of the equation.
If you’re trying to secure equipment or want to learn more about how BIG Logistics can help you plan your ocean cargo, contact us today for more information.